How IoT Devices Can Help Manufacturers Minimize Downtime
How IoT Devices Can Minimize Downtime in a Manufacturing Plant
In today’s competitive manufacturing environment, every minute of downtime costs money. By implementing IoT devices, manufacturers can gain real-time insights into their operations, identify and resolve issues quickly, and prevent costly unplanned downtime.
In this article, we will discuss how IoT devices can help manufacturers minimize downtime. We will cover topics such as:
- How IoT devices can collect data on equipment performance
- How IoT devices can send alerts when equipment is not performing as expected
- How IoT devices can be used to schedule preventive maintenance
- How IoT devices can help manufacturers comply with regulatory requirements
By the end of this article, you will have a better understanding of how IoT devices can help manufacturers improve their operations and minimize downtime.
IoT Device | How It Can Minimize Downtime | Example |
---|---|---|
Sensors | Monitor equipment conditions and send alerts when problems arise | A sensor on a conveyor belt can detect when a belt is about to break, sending an alert to maintenance staff before the belt fails and causes downtime. |
Machine learning | Identify patterns in data to predict and prevent problems | A machine learning algorithm can analyze data from sensors on a factory floor to predict when a machine is likely to fail, allowing maintenance staff to schedule repairs before the machine breaks down. |
Automation | Perform tasks that would otherwise require human intervention | An automated system can monitor and adjust production lines, ensuring that they run smoothly and efficiently. |
How IoT Devices Can Monitor Equipment
The Internet of Things (IoT) is a network of physical devices that are connected to the internet and can collect and exchange data. In manufacturing plants, IoT devices can be used to monitor equipment performance, identify potential problems before they cause downtime, and send alerts when equipment is operating outside of normal parameters.
IoT Sensors Can Collect Data on Equipment Performance
IoT sensors can collect data on a variety of equipment performance metrics, such as temperature, vibration, and usage. This data can be used to track the health of equipment over time and identify potential problems before they cause downtime. For example, a sensor that monitors the temperature of a motor can alert plant managers if the motor is overheating, which could lead to a breakdown.
IoT Devices Can Identify Potential Problems Before They Cause Downtime
In addition to collecting data on equipment performance, IoT devices can also be used to identify potential problems before they cause downtime. For example, a sensor that monitors the vibration of a machine can alert plant managers if the machine is vibrating excessively, which could indicate a problem with the bearings. This allows plant managers to take action to prevent the machine from breaking down and causing downtime.
IoT Devices Can Send Alerts When Equipment Is Operating Outside of Normal Parameters
IoT devices can also be used to send alerts when equipment is operating outside of normal parameters. This can help plant managers to quickly identify and address problems, which can help to minimize downtime. For example, a sensor that monitors the temperature of a machine can send an alert if the temperature exceeds a certain threshold, which could indicate that the machine is overheating. This allows plant managers to take action to cool the machine down before it breaks down.
How IoT Devices Can Automate Processes
In addition to monitoring equipment, IoT devices can also be used to automate processes. This can reduce the need for human intervention, which can help to minimize downtime. For example, IoT devices can be used to monitor environmental conditions, control machinery, and schedule maintenance.
IoT Devices Can Be Used to Monitor Environmental Conditions
IoT devices can be used to monitor environmental conditions, such as temperature, humidity, and air quality. This data can be used to ensure that the environment in the manufacturing plant is optimal for production. For example, a sensor that monitors the temperature of a manufacturing plant can alert plant managers if the temperature rises too high, which could damage equipment or cause workers to become uncomfortable.
IoT Devices Can Be Used to Control Machinery
IoT devices can also be used to control machinery. This can be done through a variety of methods, such as remote control, programmable logic controllers (PLCs), and artificial intelligence (AI). For example, a sensor that monitors the level of a liquid in a tank can be used to automatically control the flow of liquid into the tank. This can help to ensure that the tank is always full, which can help to minimize downtime.
IoT Devices Can Be Used to Schedule Maintenance
IoT devices can also be used to schedule maintenance. This can be done by tracking the usage of equipment and identifying when it is due for maintenance. For example, a sensor that monitors the hours of operation of a machine can be used to schedule maintenance for the machine when it reaches a certain number of hours of operation. This can help to prevent unexpected breakdowns, which can cause downtime.
IoT devices can play a valuable role in minimizing downtime in manufacturing plants. By monitoring equipment performance, identifying potential problems before they cause downtime, and automating processes, IoT devices can help to keep manufacturing plants running smoothly.
Here are some specific examples of how IoT devices have been used to minimize downtime in manufacturing plants:
- A manufacturing plant in Germany used IoT devices to monitor the temperature of its machinery. The data from the sensors was used to create a predictive maintenance model, which allowed the plant to schedule maintenance before the machinery broke down. This resulted in a 20% reduction in downtime.
- A manufacturing plant in the United States used IoT devices to track the usage of its equipment. The data from the sensors was used to identify the equipment that was being used the most. This information was used to prioritize maintenance, which resulted in a 15% reduction in downtime.
- A manufacturing plant in China used IoT devices to automate its production processes. The devices were used to control machinery, schedule maintenance, and monitor environmental conditions. This resulted in a 30% reduction in downtime.
These are just a few examples of how IoT devices can be used to minimize downtime in manufacturing plants. As IoT technology continues to develop, we can expect to see even more innovative ways to use IoT devices to improve productivity and efficiency in manufacturing.
3. How IoT Devices Can Improve Communication
IoT devices can connect to each other and to the cloud, creating a network of interconnected devices. This network can be used to share data and information, which can help to improve communication between different parts of a manufacturing plant.
For example, IoT devices can be used to collect data on the status of machines, such as their temperature, speed, and output. This data can be used to identify potential problems before they cause downtime. IoT devices can also be used to track the location of workers, which can help to ensure that they are in safe areas and that they are not working in areas where they are not authorized.
In addition, IoT devices can be used to send alerts and notifications. For example, if a machine is running at an unsafe temperature, an IoT device can send an alert to the operator. This alert can help to prevent the machine from overheating and causing damage.
IoT devices can also be used to improve communication between different departments within a manufacturing plant. For example, an IoT device in the production department can send data to a device in the quality control department. This data can be used to ensure that the products being produced are meeting quality standards.
Overall, IoT devices can improve communication in a manufacturing plant by providing a way to share data and information between different parts of the plant. This data can be used to identify potential problems, prevent accidents, and improve the overall efficiency of the plant.
4. How IoT Devices Can Help to Prevent Accidents
IoT devices can be used to monitor safety conditions, such as the presence of hazardous gases or the temperature of machinery. This data can be used to identify potential hazards and take steps to prevent accidents.
For example, IoT devices can be used to monitor the levels of hazardous gases in the air. If the levels of these gases become too high, an IoT device can send an alert to the workers in the area. This alert can help to prevent workers from being exposed to hazardous gases and can reduce the risk of accidents.
IoT devices can also be used to monitor the temperature of machinery. If the temperature of a machine becomes too high, an IoT device can send an alert to the operator. This alert can help to prevent the machine from overheating and causing damage.
In addition, IoT devices can be used to track the location of workers. This information can be used to ensure that workers are in safe areas and that they are not working in areas where they are not authorized.
Overall, IoT devices can help to prevent accidents by providing a way to monitor safety conditions and identify potential hazards. This data can be used to take steps to prevent accidents and to reduce the risk of injuries.
IoT devices can play a valuable role in improving the efficiency and safety of manufacturing plants. By collecting data and sharing information, IoT devices can help to identify potential problems, prevent accidents, and improve communication between different parts of the plant. As IoT devices continue to evolve, they are likely to play an even greater role in the future of manufacturing.
Q: How can IoT devices minimize downtime in a manufacturing plant?
A: IoT devices can minimize downtime in a manufacturing plant by providing real-time data on the status of equipment, identifying potential problems before they cause downtime, and automating tasks that can reduce the risk of human error.
Q: What are some specific examples of how IoT devices can be used to minimize downtime in a manufacturing plant?
A: Here are some specific examples of how IoT devices can be used to minimize downtime in a manufacturing plant:
- Condition monitoring: IoT sensors can be used to monitor the condition of equipment and identify potential problems before they cause downtime. For example, sensors can be used to monitor the temperature of bearings, the vibration of motors, and the current draw of electrical components. If any of these measurements exceed preset thresholds, an alert can be sent to the plant manager or maintenance staff so that they can take action to prevent a breakdown.
- Predictive maintenance: IoT devices can also be used to predict when equipment is likely to fail. This is done by analyzing historical data on equipment performance and identifying patterns that can be used to predict future failures. By taking action to repair or replace equipment before it fails, plant managers can avoid costly downtime.
- Automated tasks: IoT devices can also be used to automate tasks that can reduce the risk of human error. For example, robots can be used to perform repetitive tasks such as welding, assembly, and painting. This can free up human workers to focus on more complex tasks, and it can also reduce the risk of mistakes that could lead to downtime.
Q: What are the benefits of using IoT devices to minimize downtime in a manufacturing plant?
A: There are several benefits to using IoT devices to minimize downtime in a manufacturing plant, including:
- Reduced downtime: IoT devices can help to reduce downtime by identifying potential problems before they cause a breakdown, and by automating tasks that can reduce the risk of human error.
- Increased productivity: IoT devices can help to increase productivity by freeing up human workers to focus on more complex tasks, and by reducing the risk of mistakes that could lead to downtime.
- Improved safety: IoT devices can help to improve safety by identifying potential hazards before they occur, and by automating tasks that can reduce the risk of accidents.
- Cost savings: IoT devices can help to save money by reducing downtime, increasing productivity, and improving safety.
Q: What are the challenges of using IoT devices to minimize downtime in a manufacturing plant?
A: There are a few challenges to using IoT devices to minimize downtime in a manufacturing plant, including:
- Cost: IoT devices can be expensive, so it is important to weigh the cost of the devices against the potential benefits.
- Security: IoT devices are connected to the internet, so they are vulnerable to cyberattacks. It is important to take steps to protect IoT devices from security threats.
- Integration: IoT devices often need to be integrated with existing systems, which can be a challenge. It is important to have a plan for how IoT devices will be integrated with existing systems.
Q: How can I get started using IoT devices to minimize downtime in my manufacturing plant?
A: If you are interested in using IoT devices to minimize downtime in your manufacturing plant, here are a few steps to get started:
1. Identify your needs: The first step is to identify the specific needs of your manufacturing plant. What are the areas where you are experiencing the most downtime? What are the goals you hope to achieve by using IoT devices?
2. Research IoT devices: There are a wide variety of IoT devices available on the market, so it is important to do your research to find the devices that are right for your needs. Consider factors such as the cost of the devices, the security features, and the ease of integration with your existing systems.
3. Implement a plan: Once you have selected the IoT devices you want to use, you need to develop a plan for how they will be implemented in your manufacturing plant. This plan should include details on how the devices will be installed, how they will be integrated with your existing systems, and how they will be used to monitor and improve operations.
4. Monitor and evaluate: Once the IoT devices are in place, you need to monitor their performance and evaluate their impact on your operations. This will help you to identify any problems and make adjustments as needed.
By following these steps, you can get started using IoT devices to minimize downtime in your manufacturing plant.
:
IoT devices can play a vital role in minimizing downtime in manufacturing plants. By collecting and analyzing data from sensors, IoT devices can help manufacturers identify and address potential problems before they cause downtime. IoT devices can also be used to automate tasks, which can free up workers to focus on other tasks and reduce the risk of human error. By implementing IoT solutions, manufacturers can improve efficiency, reduce costs, and improve product quality.
Here are some key takeaways from this article:
- IoT devices can collect and analyze data from sensors to identify potential problems before they cause downtime.
- IoT devices can be used to automate tasks, which can free up workers to focus on other tasks and reduce the risk of human error.
- IoT solutions can help manufacturers improve efficiency, reduce costs, and improve product quality.
If you are a manufacturer looking to minimize downtime, IoT devices can be a valuable asset. By implementing IoT solutions, you can improve your operations and achieve your business goals.
Author Profile
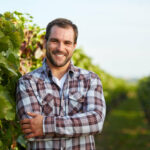
-
Meet Arthur Cook, the heart and soul behind Plant4Harvest.com. Arthur’s story is deeply rooted in the rich soil of a small American town, where the horizon is wide, and the values of hard work and connection to the land run deep. Born and raised in the quaint town of Elkmont, Alabama, Arthur’s journey in agriculture began in the sprawling fields of his family’s farm, a stone’s throw away from the Tennessee border.
Arthur’s thirst for agricultural knowledge led him to Auburn University, where he majored in Agricultural Science. During his college years, Arthur dedicated his summers to working on local farms, gaining practical experience in modern farming techniques. His academic and real-world experiences combined to give him a unique perspective on the challenges and opportunities in American agriculture.
Arthur Cook is more than just a farmer; he is an advocate for sustainable agriculture and a mentor to the next generation of farmers. Through Plant4Harvest.com, he continues to inspire, educate, and engage with a community of individuals who share his love for the land and commitment to preserving it for future generations.
Latest entries
- January 30, 2024PlantingWhen to Plant Onions in Zone 6: A Guide
- January 30, 2024GardeningWhy Do You Ache So Much After Gardening?
- January 30, 2024Tree NurturingWhen to Prune Fruit Trees in Utah for Maximum Yield
- January 30, 2024General Blog (Plants)How to Grow Tillandsia Air Plant Seeds: A Complete Guide